Best preventive maintenance scheduling software systems of 2025
Key Takeaways
- The integration of IoT and preventive maintenance software allows for real-time equipment monitoring and proactive maintenance, drastically minimizing unplanned downtimes and disruptions.
- Centralizing data flow from IoT sensors to cloud platforms simplifies asset management, improves predictive analytics and enables smart decision-making for maintenance technicians.
- Instead of using a reactive approach, businesses achieve greater equipment reliability, reduced costs and increased productivity.
- Smart sensor choice, sturdy connectivity, insightful data interpretation, automated workflows and scalable architecture are all needed to make IoT work for you – and to work long into the future.
- Implementation challenges include maintaining data security, integrating with existing systems, and delivering continuous training and support to foster team adoption.
- Next gen AI-driven analytics, digital twins and sustainability-focused strategies are redefining facility maintenance — realizing an ROI through reduced downtime, labor optimization and asset longevity.
Preventive maintenance scheduling software systems are platforms that automate, track, and optimize recurring maintenance tasks for facilities, equipment, and infrastructure. These systems allow technical teams to stay ahead of wear, compliance, and downtime by leveraging rule-based scheduling, asset tracking, and real-time notifications.
Large scale organizations build their business on these solutions to minimize unplanned downtime, manage operational budgets, and maximize asset lifespan throughout dispersed fleets. Typical functionalities involve proactive work order issuance, maintenance calendar visualization, and analytics panels that guide resource deployment.
For engineering leaders, the right preventive maintenance scheduling software can be the difference between putting out breakdown fires and maintaining predictable high-performance operations. The next few sections discuss key system features, integration approaches, and ROI tracking.
What is IoT-Powered Maintenance?
IoT-powered maintenance combines IoT data with preventive maintenance scheduling software for intelligent asset management. Harnessing connected sensors, centralized analytics, and real-time insights, organizations can move from reactive to proactive maintenance. This approach dramatically minimizes unplanned downtime and boosts operational efficiencies across industries.
The Core Concept
IoT-powered maintenance is all about injecting smart sensors into physical assets and machinery. These sensors collect real-time readings of metrics such as temperature, vibration, energy consumption, and run-time hours, offering a real-time health check of each asset.
This data feed allows the platform to proactively initiate such preventive work orders or alerts when there are early signs of wear or abnormal behavior. Rather than waiting for machines to fail, maintenance can intervene just in time, prolonging equipment life and avoiding expensive repairs.
The real magic is moving from putting out fires to a proactive data-driven workflow. Centralized dashboards and scheduling tools put every maintenance task, history, and upcoming intervention into one interface, simplifying coordination for teams managing hundreds of assets.
The Data Flow
IoT sensors communicate data through the air to a central gateway, then to cloud maintenance management systems. This frictionless data flow is the foundation of predictive maintenance.
Machine-learning-powered advanced analytics engines analyze raw sensor input, identifying patterns and foreseeing failures before they occur. For instance, too much vibration in a motor can indicate bearing wear weeks ahead of a fault.
With years of sensor data stored and analyzed in the cloud, historical trends and performance benchmarks can be leveraged and applied to optimize maintenance strategies over time. An automated data pipeline is crucial. If sensor data is lost or delayed, predictive accuracy drops and maintenance scheduling returns to guesswork.
Cloud infrastructure enables scalable storage and fast processing for organizations of all sizes.
Proactive strategies increase reliability and asset lifespan. Teams waste less effort on fire-fighting and more on strategic enhancements. This real-time asset health visibility gives leaders the ability to make smarter decisions, resource, and optimize maintenance cycles.
How to Integrate IoT with PM Software
Integrating IoT into PM software is a challenging, high-value project. Clear integration goals like minimizing downtime or enhancing asset reliability are essential from the beginning. Success requires not only technology alignment, but true collaboration between IT, maintenance, and management teams.
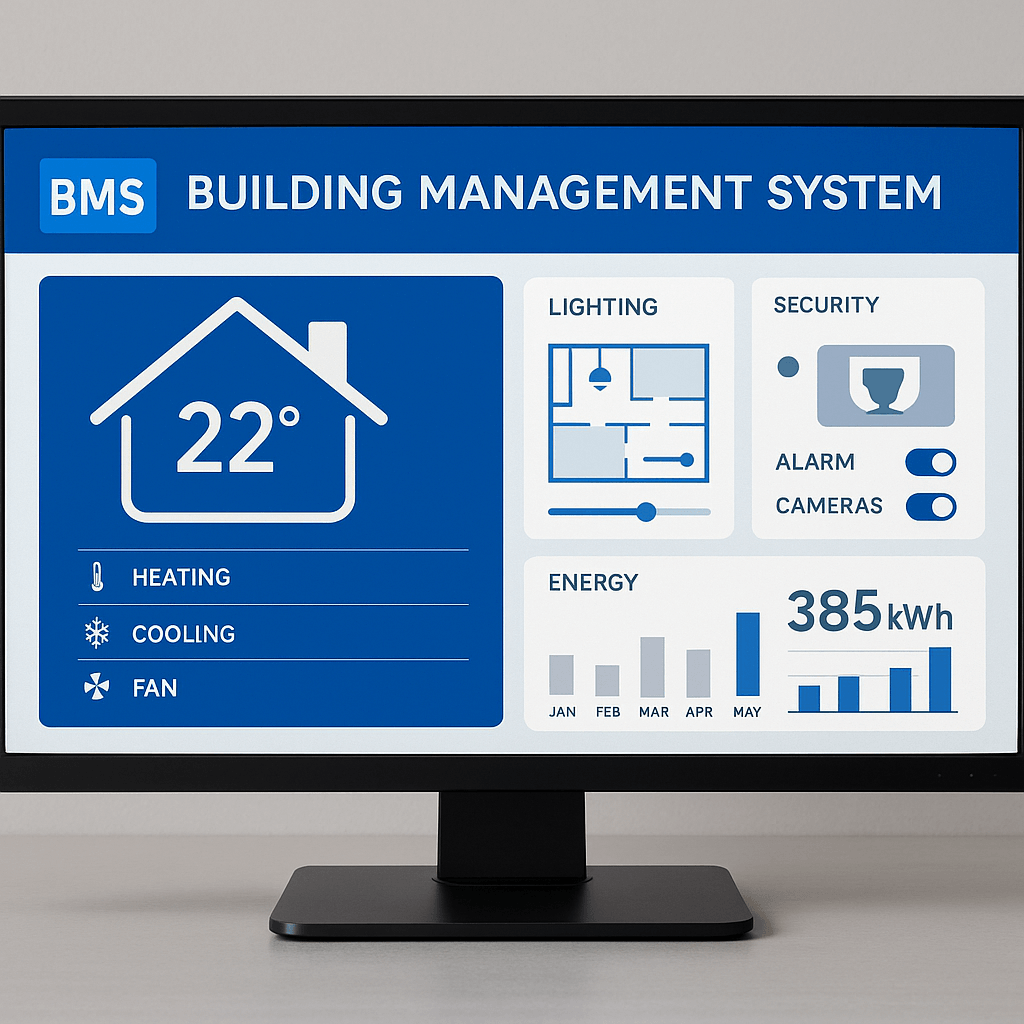
Here’s a step-by-step approach that strikes a balance between technical depth, developer experience, and business scalability.
- Define clear integration objectives tied to business goals.
- Assess existing maintenance workflows and identify integration points.
- Select IoT sensors and ensure compatibility with current systems.
- Establish secure and reliable data connectivity.
- Bridge devices to your PM platform through API-based architecture.
- Implement performance analytics for actionable insights.
- Test and validate the integrated environment thoroughly.
- Train teams and provide ongoing support for adoption.
1. Sensor Selection
Scoping sensor requirements begins by taking a close look at your assets and their maintenance needs. For instance, vibration sensors are ideal for rotating equipment, while temperature sensors are good for monitoring HVAC systems.
Interoperability counts—standard protocols (e.g., MQTT, OPC UA) guarantee sensors integrate with nearly any open-source or commercial CMMS software. Sensor scalability is not optional. Opt for modular systems that introduce new device types without re-architecting.
Pilot testing is a must. Install sensors in a test bed, and measure signal robustness and data integrity compared to standards. Test real-world effectiveness prior to expansion.
2. Platform Connection
Robust connectivity between IoT sensors and PM software fuels the whole ecosystem. Standard protocols such as MQTT, HTTP(S), and CoAP help with real-time data transmission.
Focus on API-first platforms to integrate with third-party systems and allow for future-proof extensions. While integrating, data integrity is key. Additionally, employ checksums, encryption, and validation routines to avoid data loss or corruption during transmission.
Auth and granular permissions should be available via APIs to secure access between devices and software components.
3. Data Interpretation
Maintenance teams need to be trained to interpret sensor data. Data visualization tools such as Grafana or Power BI aid in demystifying massive datasets, allowing outliers or trends to immediately stand out.
Dashboards provide real-time summaries of KPIs like mean time between failures or asset utilization. Periodic audit of your data interpretation processes to help you catch inconsistencies and refine workflows.
4. Workflow Automation
IoT-powered automation minimizes manual input. Sensor thresholds can trigger routine inspections, condition-based alerts, and work order creation. This switch simplifies reaction, reduces lag, and avoids expensive downtime.
Automated alerts provide technicians with actionable insights.
5. System Scalability
Pick IoT stacks and PM software that scale. Scalable back-end architecture adjusts for growing data and new sensor deployments. Design for scale from project launch—pluggable APIs, modular architecture, and cloud-native infrastructure minimize upgrade resistance down the line.
Essential Software System Features
Good preventive maintenance scheduling software helps technical teams maximize asset uptime, remove manual admin, and access actionable insights. At their best, platforms will couple automation with powerful analytics and open APIs, built for scalability and integration.
Key features include:
- Automated work order generation and scheduling
- Real-time dashboards with customizable KPIs (uptime, MTBF, cost)
- Predictive analytics using historical and IoT data
- Mobile accessibility for field technicians
- Inventory management with location tracking
- Automated data entry and reminders
- Customizable reporting and export tools
- Robust customer support and API-first design
- Remote monitoring and streamlined parts procurement
Automated Work Orders
Automated work orders are core. They schedule tasks according to time, sensor inputs or usage limits—eliminating human forgetfulness and admin overhead.
Automation decreases administrative overhead by streamlining redundancy in a digital environment. Maintenance teams waste less time on paperwork and more on core tasks.
For example, integrating the IoT sensors kicks work orders automatically if vibration or temperature exceeds preset thresholds — ensuring interventions happen well before failure.
To keep your teams aligned and accountable, real-time status updates on work orders — in progress, completed or delayed. Automated reminders keep you from missing deadlines, which further reduces unplanned downtime.
Real-Time Dashboards
Real-time dashboards provide maintenance leaders immediate insight into operations. They show live metrics for equipment uptime, maintenance costs, inventory and open work orders.
By monitoring KPIs such as MTBF, cost per repair, or overdue tasks, managers can quickly spot bottlenecks or recurring problems. Custom dashboards allow every facility to showcase metrics that matter locally–one plant monitors spare parts turnover, another monitors water leak alerts.
Decision-making benefits from having actionable data always at hand. Dashboards speed up your root cause analysis and allow you to prioritize data-driven decisions, particularly across distributed or global portfolios.
Predictive Analytics
Predictive analytics uses past maintenance data and sensor data to anticipate future requirements. Leveraging machine learning models, the software detects anomalies in equipment failure, allowing it to be serviced before it breaks down.
It’s this approach that dramatically reduces unscheduled breakdowns and cost overruns. By retraining these models on a regular basis, changing operational conditions — such as increased equipment load or shifts in the environment — are incorporated.
Teams enjoy ongoing system learning, increasing dependability and longevity of the assets.
Mobile Accessibility
Field technicians require mobile access to create, update and close work orders on the go. Mobile apps streamline communication, teams status update or part request in real time, management monitor progress remotely.
Real-time data entry removes paperwork and lags, reducing mistake rates. Mobile tools record maintenance history and inventory transactions at the point of origin.
Mobile accessibility is a baseline, not a luxury.
Overcoming Implementation Hurdles
Preventive maintenance scheduling software systems hold great promise, but implementation is rarely straightforward. Teams grapple with challenges such as legacy infrastructure, data migration and cultural resistance. Thoughtful planning, vendor cooperation and continuous support are the secret to maximizing system value.
Data migration from legacy systems is notoriously error-prone. A detailed mapping and staged import reduce the risks. Not to mention ensuring compatibility with existing IoT and automation infrastructure, which is non-trivial. Open API-first platforms assist in this regard.
Data security and privacy issues balloon with IoT integration. Encryption and audits frequently become necessary to safeguard sensitive information. Staff resistance can hinder adoption. Continued training and change management fuels adoption.
Vendor backing and community resources are often underrated yet critical for troubleshooting and upgrades. Real-time system performance monitoring and safeguards ensure that operations will not be interrupted while in transition. Phased rollouts restrict disruption and help maintain operational continuity.
Data Security
Maintenance data is a premium target for cyberattacks, particularly with ubiquitous IoT deployment. Strong encryption—at rest and in transit—should be standard. Device-to-cloud transmission must be secured with a standard communication protocol such as TLS 1.3 or SSH.
IoT device hardening, like turning off unused ports and implementing multi-factor authentication, decreases attack surfaces. Regular security audits (quarterly at minimum) are needed to surface vulnerabilities, with penetration testing providing real-world assurance.
While community-backed, open-source alternatives tend to patch more quickly and provide transparency, they necessitate rigorous updating routines. Automated alerting for unusual network activity can catch breaches early, enhancing overall security posture.
System Integration
Integration with legacy maintenance databases and proprietary field devices is seldom smooth. Compatibility is easiest solved by adopting platforms with wide protocol support (e.g., MQTT, OPC UA, RESTful APIs). You might need custom middleware or adapters for edge cases.
Interdepartmental communication—getting IT, operations, and maintenance in the same room—avoids expensive misalignments. Phased rollouts, like piloting with a single asset class, allow teams to debug in production without endangering a broad downtime.
With well-documented APIs and open-source SDKs, integration becomes a breeze. This enables legacy-to-modern migration one piece at a time, facilitating a smoother transition.
Team Adoption
Engagement starts early. Designing with maintenance leads in requirements gathering builds ownership. Resistance is natural, so openness about the system’s objectives and job effects is key. Peer-led training, aided by vendor-provided resources, reinforces abilities and confidence.
Continuous feedback loops—like user surveys and open forums—surface adoption bottlenecks. By acknowledging these small wins, whether it’s less manual scheduling or faster fault detection, you create momentum that fuels buy-in.
Continued support, both technical and emotional, maintains momentum during the transition. This ongoing encouragement is essential for ensuring long-term success and user satisfaction.
The Future of Facility Maintenance
Facility maintenance is being reinvented. New tools and systems are enabling teams to maximize uptime, reduce costs and achieve business goals, even as resources become scarce. The industry is evolving towards automation, data-driven approaches, and sustainability, fueled by reliable, open-source technologies.
AI-Driven Decisions
AI adds new power to analyze maintenance data, extracting insights from millions of sensor events, work orders and usage logs. This allows teams to transition from reactive fixes to data-driven decisions that focus on critical assets.
As an example, AI can surface hidden patterns in chiller run times or elevator fault codes, enabling smarter resource allocation. Sophisticated algorithms now fine-tune schedules by tracking live equipment usage, weather information, and occupancy patterns.
Thus, maintenance windows shrink and downtime drops – vital when an hour offline can cost a manufacturing plant $260,000. AI models predict failures with anomaly detection, allowing teams to intervene before expensive breakdowns affect operations. More than 55% of facility managers already harness AI for these activities, simplifying workflows and minimizing manual overhead.
By betting on open-source, API-first AI solutions, you’re ensuring flexibility and scalability. Teams can plug these tools into existing CMMS or IoT platforms, combining them with established best practices and strong security standards.
Digital Twin Synergy
Digital twins are virtual replicas of physical assets employed for tracking and examination. With live sensor data synced to these models, teams can visualize asset health, simulate wear and plan interventions.
By simulating maintenance, it can help allocate labor and spare parts efficiently. For instance, scenario testing might uncover when to service HVAC systems given past performance and anticipated demand.
Digital twins enable ongoing feedback—every maintenance job completed updates the model, making future predictions even more precise. Embracing digital twins fosters a culture of iteration. Teams receive a sandbox to trial modifications prior to implementing them, lessening risk and increasing the speed of innovation.
Sustainability Goals
IoT-powered maintenance is at the heart of smashing sustainability goals. Smart sensors track energy consumption and environmental changes, allowing real-time optimization that reduces waste.
It cuts down on wasted part replacements and saves energy because it only services when required. Tracking emissions standards compliance is becoming ever more important as regulations tighten globally.
Making maintenance part of your sustainability initiatives drives tangible business value and supports teams in achieving their ESG goals.
Measuring Your ROI
ROI needs to be precisely measured to make data-driven decisions about investing in preventive maintenance scheduling systems. Instead, stakeholders should emphasize pragmatic, replicable measures of the actual business impact of IoT-powered O&M platforms, favoring open, API-centric solutions that tie into existing tools and workflows.
- Downtime reduction: Track total machine downtime (in hours/month) before and after implementation.
- Labor optimization: Monitor total labor hours spent on maintenance tasks and overtime costs.
- Asset lifespan: Measure average years of service per asset. Compare before and after.
- Cost savings: Calculate direct savings from reduced emergency repairs, inventory, and utilities.
- Compliance: Evaluate audit scores or compliance incident rates.
- Inventory turnover: Monitor frequency of parts and supplies usage.
- Energy consumption: Track energy savings tied to asset performance improvements.
Downtime Reduction
Downtime is engineering teams’ most glaring pain point. IoT integration makes real-time monitoring a reality, with systems automatically flagging anomalies before failure. This proactive stance can reduce machine downtime by 30-50%, matching the best in industry and liberating capacity for growth projects.
The financial impact is significant: for every dollar spent on preventive maintenance, up to five dollars can be saved by avoiding costly emergency fixes and lost production. Companies with mature PM programs often experience 12-18% lower total maintenance costs, and they report less unplanned outages, which stabilizes their revenue streams.
By defining clear downtime minimization goals—reducing outages by 20% or eradicating unplanned shutdowns—creates an accountability structure. Following these targets with standardized measures (e.g., MTBF, MTTR) simplifies demonstrating your ROI and arguing for more investment.
Labor Optimization
Smart scheduling driven by IoT data ensures labor dollars are deployed precisely where they are needed, avoiding unnecessary downtime and overtime. Automation of ticket assignment and scheduling keeps maintenance teams from being overwhelmed at peak times.
This increases productivity, as real-time workload information allows you to shift staffing as demand unexpectedly spikes. For instance, connecting with open-source workforce management APIs can automate shift scheduling, cutting labor costs and boosting team spirit.
Fine-tuning labor deployment results in less firefighting, fewer midnight crisis phone calls, and more time for dreaming up bold initiatives. These operational efficiencies translate directly to measurable ROI.
Asset Lifespan
Regular preventive maintenance, guided by IoT insights, can add 20-40% to the life of equipment. A $75,000 piece of equipment used over 10 years that has its life extended by just 6 months generates a savings of $3,750—and that’s not even counting the value of delayed capital expenditure.
IoT-empowered insights tailor maintenance activity to the asset’s actual status, rather than predetermined schedules, optimizing resource utilization and minimizing over-maintenance. Get more uptime, less replacement cycles and more stable operating budgets.
Over time, analyzing asset performance data on a routine basis sustains strategic planning. This is the way technical teams provide enduring business value and reinforce their justification for investment.
Conclusion
In short, IoT-enabled preventive maintenance scheduling software systems provide a tangible route toward elevated reliability and predictable cost management in facility operations. Team members get real-time asset visibility, automated work order management, and smarter resource allocation. By integrating IoT data, you can eliminate guessing when it comes to maintenance and empower organizations to address problems before they interrupt operations. Most early technical challenges are related to integration and change management, not the technology. As facility maintenance matures toward predictive, data-driven models, these systems anchor a foundation for scaling operations and rationalizing investment. For CTOs and engineers, it’s a strategy that moves you away from putting out fires towards long-term asset value and operational excellence, supported by clear metrics and insights.
Frequently Asked Questions
What is preventive maintenance scheduling software?
Preventive maintenance scheduling software systems help you to plan, track and automate maintenance tasks. It gets equipment serviced on a regular schedule, which prevents breakdowns and prolongs asset life.
How does IoT improve preventive maintenance scheduling?
IoT sensors gather real-time data from machinery. This information aids software in foresight maintenance scheduling, allowing it to anticipate problems and plan repairs in advance, avoiding downtime and expenses.
What features should I look for in preventive maintenance software?
Key features are asset tracking, automated alerts, work order management, integration with IoT devices, and easy reporting. These capabilities increase productivity and visibility.
Can preventive maintenance software integrate with existing systems?
Yes, as with most modern preventive maintenance systems, it offers integration with other software and IoT platforms. Which streamlines data sharing and enhances decision-making.
What are common challenges in implementing IoT-powered maintenance software?
Issues such as data security, upfront cost, staff training and system compatibility continue to be hurdles to overcome. Financial planning and picking scalable, secure solutions can get past these hurdles.
How can I measure the ROI of preventive maintenance software?
Quantify ROI by monitoring minimized downtime, decreased repair expenses, extended equipment life, and enhanced output. Quality software offers integrated analytics to track these metrics.
Is preventive maintenance scheduling software suitable for all facility sizes?
Yup, preventive maintenance software is scalable. It helps small facilities and large organizations optimize maintenance planning and resource allocation.